Electron beam evaporation of substances in vacuum differs from other methods of vacuum evaporation, namely thermal and ion plasma evaporation, primarily by its versatility, technological flexibility and cost-effectiveness. The electron beam is one of the most effective heat sources. During collision of a flying electron with a solid surface the electron kinetic energy is converted into thermal energy in a thin surface layer of 1 to 2 µm thickness. Therefore using a focused electron beam the heat source is located within the solid proper, and provides for the maximum degree of electric energy conversion into thermal energy.
Modern electron guns of 50 to 100 kW power allow evaporation of metallic and non-metallic substances at highly efficient rates of approximately up to 10-2 g?cm-2?s-1.
At evaporation in vacuum of 10-2 - 10-4 Pa the spatial density of the vapour flow above the evaporator follows a cosinusoidal law of distribution, according to which the maximum density is observed in the direction of a normal to the evaporation surface (angle α = 0). At vacuum lowering to 1 Pa, for instance, with bleeding argon into the chamber, the vapour flow is scattered in the direction of a more uniform density distribution.
Evaporators consisting of a copper water-cooled crucible (cylinder), which accommodates the evaporation material in the form of an ingot (cast or compacted) of 25 to 70 mm diameter became the most widely accepted. The level of liquid pool surface from which evaporation starts, in most of the variants, is kept constant by the mechanism of vertical displacement of the ingot.
During evaporation of 70 mm ingot, the rate of vapour flow condensation on a flat stationary substrate located above the liquid pool surface at 300 mm distance, can be up to 30 to 50 µm/min for metals and alloys and 15 - 20 µm/min for ceramics (oxides, carbides, borides).
Fig.1a and 1b show the schematics of electron beam evaporation of substance A from one source and of A and B from two sources. Naturally, condensation surfaces can be flat, cylindrical, or of a more complex shape, stationary or making certain motions in space, using the respective mechanisms for motion transfer.
The schematic in Fig.1b corresponds to the technological process of deposition of a two-component material AB on a flat surface in the form of a disc rotating around a vertical axis. Substrate rotation is required to produce a uniform composition across the condensate thickness. It should be noted that such a technological process can be readily transformed into a process of producing multilayer condensates of A/B type by placing a partition between the sources (noted by a dashed line). At a constant rate of evaporation of substances A and B, the speed of substrate rotation will be a simple and reliable technological parameter for controlling the thicknesses of alternating layers A and B.
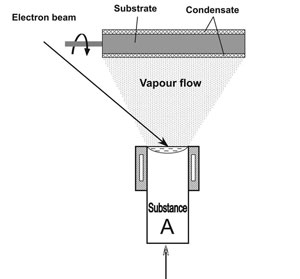
|
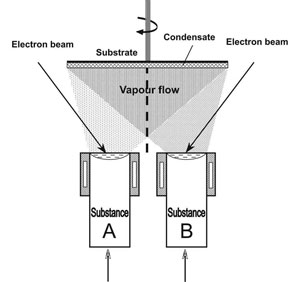 |
a) |
b) |
Fig.1. Technological schematics of evaporation and condensation of substances: from one source (a) and two sources (b). |
Developed laboratory and production units have 3 or 4 independent evaporators (water-cooled crucibles) and respective electron beam guns for evaporation of 3 to 4 substances by a preset program.
Similar to pure metals, alloys evaporate in the form of individual atoms. For most of the alloys, however, the composition of the vapour phase above the melt does not correspond to the average melt composition. Alloy fractionation occurs, namely the condensate layers adjacent to the condensation surface, contain the maximum amount of volatile components. Condensates of multicomponent metallic materials chemically homogeneous across the thickness, are obtained using different evaporations techniques, including evaporation of individual alloy components from independent sources.
Evaporation of compounds (oxides, carbides, borides, etc.) is usually accompanied by a change of the initial molecule form. Dissociation of the initial molecules with formation of gaseous products is characteristic for many refractory compounds. For instance, O, Al, AlO3, Al2O form at Al2O3 evaporation. Producing condensates by direct evaporation from one source without a change in the initial composition of the compounds is only possible under the condition that the dissociation products have practically the same volatility, i.e. a coordinated "congruent" evaporation of the compounds is required. Refractory oxides (Al2O3, Y2O3, ZrO2, MgO), carbides (TiC, ZrC, SiC, NbC), borides (TiB2, ZrB2) can be evaporated from copper water-cooled crucibles using electron beam heating practically without any change of the composition. A number of compounds, for instance, WC, Si3N4, TiN, ZrN cannot be deposited through direct evaporation, as they decompose on heating with formation of products with markedly different volatility. Such compounds in the form of condensates can be obtained by component evaporation from two independent sources (W and C) or using the so-called reactive evaporation with bleeding of the respective gas to the working chamber and vapour flow ionization.
The "hot pool" method widens the capabilities of direct electron beam evaporation of metallic and non-metallic materials from one source. For instance, at evaporation of ingots of Ni-Cr, Ni-Cr-Al alloys with Y or Ti additives with a lower vapour pressure at evaporation temperature, the latter do not go into the vapour phase, but accumulate in the liquid pool as the ingot evaporates. This phenomenon can be eliminated, if a Nb tablet is placed on the ingot surface before evaporation, based on achieving 25 - 30 wt.% Nb in the future liquid pool. Then a liquid pool with a higher evaporation temperature is formed at melting of the ingot end face, ensuring transition of the additives into the vapour phase and the condensate without disturbing the pool stability (local boiling or spatter). Nb does not evaporate, and its content in the liquid pool remains practically unchanged. Therefore, after ingot evaporation the solidified "hot pool" in the form of a flat tablet is transferred to the end face of the next ingot, and this cycle can be repeated many times.
Another example is carbon evaporation from a liquid pool of tungsten. In this variant, W tablet is placed at the end face of a compacted graphite rod of 25 to 70 mm diameter. After tungsten melting a stable liquid pool is formed, and a stable continuous transfer process is established, namely graphite dissolution in the liquid pool volume, its evaporation from the liquid pool surface and condensation on the specified surface. Rates of evaporation of a graphite rod of 70 mm diameter in this process are up to 1 kg/h, the corresponding rates of condensation on substrates located at 280 - 300 mm from the pool surface are equal to 30 - 40 µm/min. Tungsten practically does not evaporate from the liquid pool. Therefore, a W tablet can be used many times, similar to the above example.
Multicomponent condensates with a gradient of composition and structure can be obtained by evaporation from one source of compacted powder mixtures in the form of small ingots (tablets) of the following type:
A - B - C - D - ... ,
for which the vapour pressure at the evaporation temperature decreases in the direction from A to D. Components A and B can be powders of metals or alloys, C and D - powders of refractory oxides. For instance, Al-Cr-Al2O3-ZrO2. Al is the first to evaporate, followed by Cr and then Al2O3 and ZrO2.
Other variants of graded condensates consisting of different combinations of metallic, metal-ceramic and ceramic layers can be obtained by evaporation of a composite ingot from one source. Fig.2 shows the schematic of the structure and general view of a composite ingot. Composite ingot, preferably of a cylindrical shape, consists of a ceramic base, and individual fragments (inserts) of metallic and non-metallic materials of the necessary shape and dimensions, selected and located in the ingot volume so that a graded condensate of the specified composition and structure is formed on the substrate at continuous evaporation and subsequent condensation of the vapour phase.
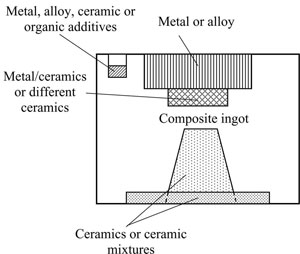 |
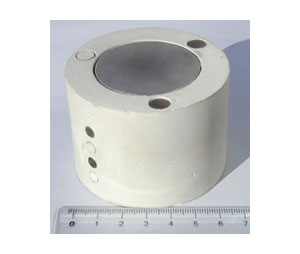 |
a) |
b) |
Fig.2. Scheme (a) and general view (b) of composite ingot. |
Composition and structure of the future condensates are programmed in the above powder tablets and composite ingots.
Substrate temperature TS is one of the main technological parameters determining the condensate structure. Atoms (molecules) of the vapour flow, having a certain kinetic energy, while colliding with the condensation surface, go into an adsorbed state, and, exchanging energy, interact with the surface. Surface temperature determines the level of thermal activation of an adsorbed atom.
It is experimentally established that three characteristic structural zones with boundary temperature T1 and T2 form at direct electron beam evaporation of pure metals and refractory compounds of the type of oxides, carbides, borides and subsequent condensation of the vapour flow on substrates in a broad range of temperatures TS. Fig.3 gives the schematic of the structural zones depending on homological temperature TS/Tm (Tm is melting temperature of the condensed substance in Kelvin). For instance, for condensates of pure nickel average values of boundary temperatures are equal to: T1 = 270°C; T2 = 450°C.
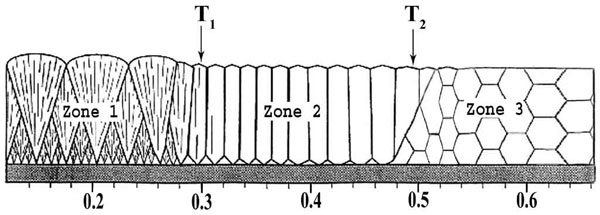 |
Homologous Temperature TS/Tm |
Fig.3. Schematic of condensate structure depending on substrate temperature TS. |
In the low-temperature zone (TS < T1) the condensates have an amorphous or nano-sized structure. In the second zone (T1 - T2) the condensates are characterized by a columnar structure with the predominant crystallographic orientation. The width of columnar crystallites increases from tens of a micrometer up to several micrometers with temperature rise in the range of T1 - T2.
Non-equilibrium condensate structures in these zones are also characterized by nano- and microsized porosity, dependent on individual properties of substances and technological parameters of deposition, primarily, substrate temperature, deposition rate, orientation and motion of the substrate relative to the vapour flow.
In the high-temperature third zone (TS > T2) the columnar structure transforms smoothly into the equiaxed grain structure. Grain size increases with increase of temperature TS. For instance, for pure nickel condensates at TS = 850°C, the average grain size is equal to 70 - 75 µm.
It should be noted that at the vapour flow collision with the smooth surface of W or Ta preheated up to temperature TS, higher than 0.75 - 0.80 of the melting temperature of evaporation metals, carbon or stable ceramics (Al2O3, ZrO2) condensation disruption occurs, i.e. re-evaporation with vapour flow reflection approximately by the law of optics: angle of beam incidence is equal to the angle of reflection to the normal of reflection density. For instance, at condensation rate of 10 µm/min for Cu, Ni, Fe, Ti, Al2O3, C, ZrO2, the temperatures of condensation disruption are equal to, respectively: 1000°C, 1200°C, 1400°C; 1580°C; 1700°C; 1800°C and 1900°C.
Vapour phase reflectors widen the capabilities of condensation on the surfaces beyond the zone of action of the main vapour flow, for instance, on the reverse side of a metal strip or wire, and are also effective in special condensation methods to produce a powderlike deposit.
Energy of atoms flying to the substrate, as well as those adsorbed by the substrate, and, therefore, the structure and properties of condensates produced by direct electron beam evaporation, can be varied in a certain range, by addition of ionized and accelerated atoms and molecules to the vapour phase.
First of all, it is necessary to consider the combined process of deposition with partial ionization of the vapour flow, using a circular electrode, located above the liquid pool surface in the evaporator. Low-voltage arc discharge is excited in the vapour flow between the electrode and pool surface. The substrate has a negative potential (bias) of the order of 100 - 500 V. Positive ions of evaporation material, flying to the substrate, acquire additional energy and increase the pulse energy at collision with the substrate. Depending on evaporation material, and technological process conditions, argon can be bled into the working chamber at the pressure of about 0.5 Pa for stabilization of the arc discharge and formation of additional heavy ions of argon or reactive gas, for instance, nitrogen, for synthesis of the respective nitrides on the condensation surface.
Self-sufficient sources of accelerated ions, for instance, of magnetron type, are also quite promising. Ion source position in the working chamber independent on the electron beam evaporator, allows performing controllable bombardment with accelerated ions of argon or other gases, primarily, of the initial deposition surface with the purpose of its cleaning and activation, as well as condensation surface during condensate formation.
Controlling the process parameters of vapour phase deposition on substrates allows producing two main kinds of condensates:
-
Condensates in the form of foil, sheet, plates or items of a more complex shape, separated from substrates after deposition. These are materials and semi-finished products. Their separation from the substrates is provided, primarily by preliminary deposition of thin (3 - 5 µm) anti-adhesion layers, for instance CaF2 on the substrates.
-
Condensates in the form of relatively thin (1 - 500 µm) functional coatings or thicker (> 500 µm) structural coatings with a high strength of adhesion to the surface of the item or semi-finished product.
In conclusion, it should be emphasized once more, that the evaporation and condensation processes realized in a vacuum of 10-3 - 10-2 Pa (7.5 · (10-6 - 10-5) Torr) are perfect in ecological terms, as they practically do not generate any harmful evolutions into the atmosphere.
|