Investigations of the structure and properties of many inorganic, metallic and non-metallic materials deposited from the vapour phase, i.e. thick condensates separated from substrates, have been performed over the last 35 - 40 years.
Fig.4 schematically shows structures of these materials. Dimensions and shapes of the structural elements (grains, phase particles, pores, layer thickness) can be varied within a broad range from nanometers to micrometers by varying the deposition process parameters.
1. Single-phase |
2. Multiphase |
3. Multilayer |
4. Porous |
5. Graded |
6. Special structures (carbon nanotubes and fullerenes, quasicrystals, etc.) |
|
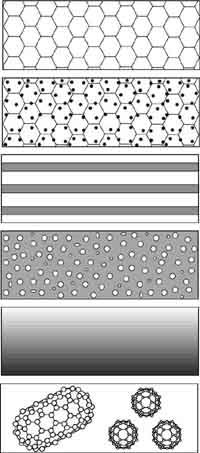 |
Fig.4. Schematics of structures of materials and coatings produced by vapour phase deposition |
Fig.5 shows as an example dependencies of the main mechanical properties, namely ultimate strength σB, microhardness Hµ and ductility ε (elongation at fracture) on substrate temperature Ts of nickel condensates 1.0 - 1.2 mm thick. Condensates were produced on steel substrates of 100x240 mm size with a smooth variation of temperature Ts along the substrate in the range of 200 - 900°C. After deposition, the condensates were separated from the substrate using a thin (1 - 3 µm) separation layer of CaF2, pre-deposited on the substrate surface. As was noted (see "Basic technology" section), for Ni condensates limit temperatures T1 and T2 are equal to 270°C and 450°C, respectively. Fig.5 demonstrates that at temperature Ts ≈ T1 the condensates are characterized by a high strength, hardness and low ductility (1 - 2%). An abrupt lowering of the values of strength and hardness, and ductility increase up to 14 - 15% are observed in the range of T1 - T2. A slight lowering of strength and hardness is found at substrate temperatures Ts > 450°C. Ductility rises to 38%. These values of mechanical properties are identical to those of pure polycrystalline nickel after high-temperature annealing. Similar dependencies are also obtained for other single-phase materials, namely pure metals, alloys (solid solutions), refractory compounds (oxides, carbides, borides).
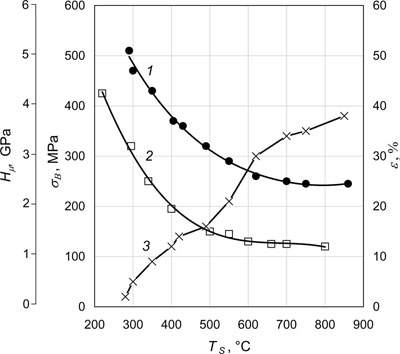 |
Fig.5. 20°C mechanical properties of nickel condensates depending on substrate temperature. 1 - ultimate strength σB, 2 - microhardness Hµ; 3 - elongation at fracture ε. |
More complex dependencies of the structure and properties are observed in two-phase condensates, containing second phase particles, for instance, a metal matrix with dispersed oxides. Substrate temperature Ts and second component content are the main parameters, determining the structure and properties of these condensates. Second component, as a rule, is added to the vapour flow of the main component (matrix) by evaporation from an independent source.
Fig.6 shows dependencies of the size of ZrO2 particles uniformly distributed in the nickel matrix, on volume fraction of ZrO2 at three substrate temperatures of 650°C, 850°C and 1100°C. Mean sizes of the particles were determined using a transmission electron microscope. As follows from the presented dependencies, the size of ZrO2 nanoparticles increases with substrate temperature and volume content of ZrO2. At temperature Ts = 650°C particles of 20 - 25 nm size are present in the practically equilibrium nickel matrix with 1 - 3 vol. %ZrO2.
It should be particularly noted that formation of the second phase nanoparticles during condensation is accompanied by a marked refinement of matrix grains. For instance, average grain size in pure nickel condensates is equal to 70 - 75 µm at Ts = 850°C, as was noted (see "Basic technology" section), while at the same temperature Ts and ZrO2content of 1.5vol.%, it decreases to approximately 4 µm. Refinement of grains (crystallites) proceeds monotonically with the increase of the second phase content.
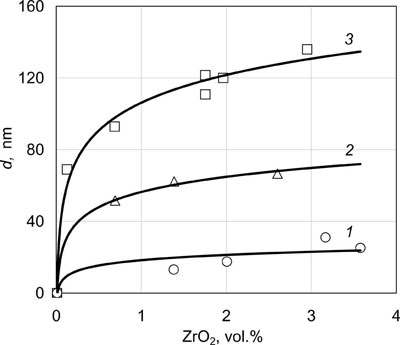 |
Fig.6. Dimensions of ZrO2 particles in Ni-ZrO2 condensates, depending on their ZrO2 content at three substrate temperatures of 650°C (1), 850°C (2) and 1100°C (3). |
Nanoparticles of oxides, carbides, borides promote an intensive refinement of grains in metal matrices of thick condensates.
A high thermal stability of the structure of condensates of the type of metal - refractory oxide should be noted. For instance, in condensates based on nickel, iron and copper, the particles practically do not grow when heated up to a temperature of 0.9Tm and soaking for 10 - 20 h.
The fine grain of the metal matrix and nano-sized hard (high modulus) particles of the second phase increase the level of the condensate mechanical properties. For instance, pure nickel condensates, produced at Ts = 650°C, have 20°C yield point σ0.2 equal to 90 MPa, and ultimate strength of 240 MPa, while condensates with 2.5vol.% ZrO2 also deposited at 650°C, have σ0.2 = 730 MPa and σB = 870 MPa. Al2O3 particles provide a more intensive strengthening.
Steady-state creep rate of these condensates at 1000°C and 50 MPa load differs by approximately 104 times: for pure nickel - 102 h-1 and nickel with 2.5 vol.% ZrO2 - 10-2 h-1.
Similar dependencies of mechanical properties were also obtained for other metal matrices. Fig.7 shows 20°C yield points of two-phase Cu-Mo and Cu-ZrB2 condensates depending on the second phase content.
When studying the interrelation of the structure and mechanical properties of two-phase condensates simultaneously with the above dependencies, two characteristic dimensional effects of the structure and mechanical properties at moderate temperatures were established.
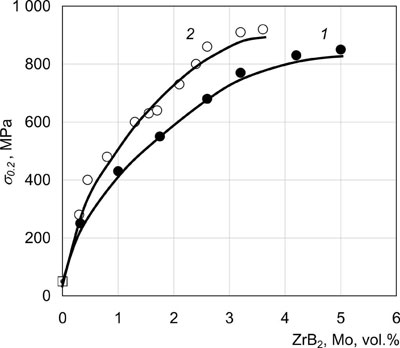 |
Fig.7. 20°C yield point of two-phase Cu-Mo (1) and Cu-ZrB2 (2) condensates. |
The first of them demonstrates the maximum ductility of the condensates, when the mean grain size or columnar crystallite width D is equal to the mean free path between the particles, Λ, i.e. structural condition is D = Λ. The second effect demonstrates the maximum strength and hardness, when the condensate contains 60 - 80 vol.% of high-modulus particles and 40 - 20 vol.% of the low-modulus second phase.
Fig.8 shows the dependencies of yield point σ0.2 and elongation at fracture ε of two-phase condensates of Ni - 20wt. %Cr + Al2O3 about 1 mm thick deposited at Ts = 900°C. Mean crystallite size D of condensates of a pure solid solution of Ni - 20wt.%Cr is equal to 60 µm. At addition of 0.14 vol.% Al2O3 it drops to 10 µm, and at 0.63 vol. % Al2O3 it is equal to 4 µm. Mean particle diameter d at 0.63 vol.% Al2O3 is equal to 40 nm.
As is known, for small volume fractions of the second phase f, (f < 0.1), the mean free path between particles is:

where d is the mean particle size. Thus, in the range of 0.50 - 0.85vol.% Al2O3 structural condition D = Λ is satisfied, and a clear maximum of elongation (ε) and minimum of yield point (σ0.2) are observed on concentration dependencies of the mechanical properties. Microhardness is also minimum in this narrow range of second phase concentrations.
Similar dependencies were also obtained in Ni-Al2O3system. Extremums of mechanical properties under the condition of D = Λ are characteristic both of the ductile metal matrices, and brittle metal (Be, Cr, Mo, W) and ceramic matrices. For instance, Cr-Cr2O3 condensates deposited at Ts = 970°C in the range of 0.3 - 0.8vol.% Cr2O3 demonstrate a clear maximum of ductility, angle of bending of flat samples being equal to 160° with minimum microhardness values of 1.25 MPa.
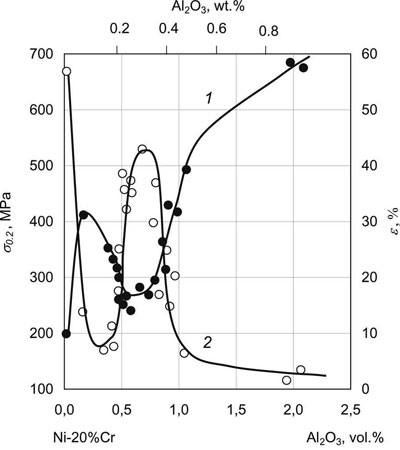 |
Fig.8. Mechanical properties of Ni - 20 wt.%Cr condensates at 20°C, depending on Al2O3 content. 1 - yield point, σ0.2, 2- elongation at fracture,ε |
Dependencies of mechanical properties with minimum σ0.2 and maximum ductility were also obtained when studying the two-phase condensates of iron, nickel and chromium with nanoparticles of low-modulus materials such as Fe-Ce2S3; Fe-CaF2; Ni-C, Cr-Cu; Cr-Y, etc.
The second extremum of mechanical properties, as was noted above, was found in two-phase condensates with 40 - 20 vol.% of the low-modulus phase. In these condensates, the second structural condition is satisfied: mean free path between particles Λ is approximately equal to the mean distance between particles, λ, i.e. Λ ≈ λ.
Fig.9a and Fig.9b give the characteristic maximums of ductility and microhardness of Fe-Cu, Cr-Cu and Mo-Cu two-phase condensates obtained by component deposition from two independent sources at substrate temperatures Ts of 600°C, 850°C and 950°C, respectively. Condensate thicknesses were 0.8 - 1.2 mm. Average size of Mo, Cr, Fe grains in the respective condensates at 20vol.% Cu is equal to approximately 1µm, the width of copper interlayer being ~ 0.3 µm. Yield point of such two-phase condensates in the above concentration range can be evaluated by the following expression:
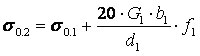
where σ0.1, G1, b1, f1 and d1 are the yield point, shear modulus, Burgers vector, volume fraction and size of particles of the high-modulus second phase, respectively.
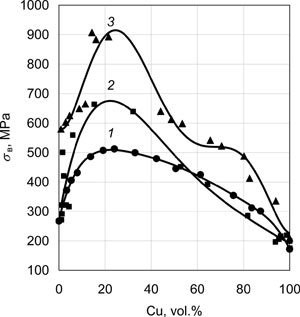 |
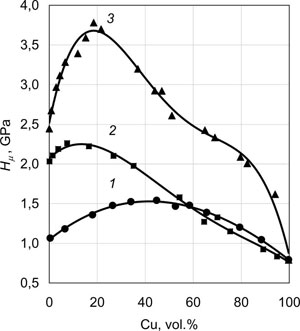 |
a) |
b) |
Fig.9. Mechanical properties at 20°C of two-phase condensates of Fe-Cu (1); Cr-Cu (2) and Mo-Cu (3), depending on copper content: ultimate strength (a); and microhardness (b). |
Ductility and fracture toughness of these condensates depend, primarily, on individual properties of the high-modulus phase, as well as its dimensions, shape and volume distribution. Intergrowing of individual particles with formation of skeletal forms markedly lowers the level of the above properties.
Such maximums of strength and hardness were obtained when studying TiC-Ti, TiC-Mo, TiC-SiC, B4C-Ti, Be-Al and other condensates. Maximum of strength of classical sintered hard WC-Co cermet provides further confirmation of the universality of the above structural condition Λ ≈ λ.
Dimensional effects of the structure and properties are also characteristic of a wide class of multilayer materials produced by electron beam evaporation of initial inorganic substances. Layer interfaces are known to be the sources of far-range inner stresses and effective barriers in the path of moving dislocations. Therefore, multilayer materials can be high-strength at room temperature, and high-temperature resistant at high temperatures. Layer thickness is one of the main parameters determining their properties.
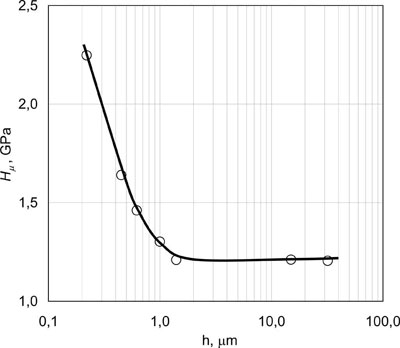 |
Fig.10. Microhardness Hµ of microlaminate Fe/Cu condensates depending on thickness h of alternating layers. |
Fig.10 shows the dependence of microhardness Hµ of bulk Fe/Cu condensates with alternating microlayers of iron and copper of the same thickness h. An abrupt increase of condensate microhardness is observed at layer thicknesses less than 1 µm. Strength properties of multilayer condensates increase in a similar manner. Investigations of mechanical properties of Fe/Cu, Cr/Cu and Mo/Cu microlaminate condensates with equal thickness of the layers showed that the interrelation of yield point σ0.2 with layer thicknesses h can be presented by the following dependence:
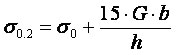
where σ0, G and b are the yield point, shear modulus and Burgers vector of the crystalline lattice of a high-modulus (load-carrying) layer of Fe, Cr or Mo. For instance, for Fe/Cu with GFe = 81 GPa, bFe = 0.248 nm, h = 0.5 µm and σ0= 150 MPa, the yield point will be equal to 750 MPa. Steady-state creep rate of equal-thickness Fe/Cu condensates at 600°C and 60 MPa stress is 100 times lower than that of pure iron.
Fig.11 shows temperature dependence of yield point σ0,2 of a bulk microlaminate Mo/Cu condensate.
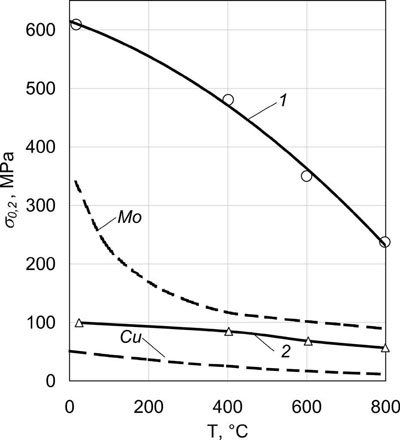 |
Fig.11. Temperature dependence of the yield point of bulk massive microlaminate Mo/Cu condensates. 1 - thickness of layers of Mo - 1.1 µm, Cu - 1.8 µm; 2 - thickness of layers of Mo - 1.1 µm, Cu - 7.0 µm. Dashed lines show yield points of pure Mo and Cu. |
Mechanical properties of microlaminate condensates of Ni16Cr5Al/10 vol.% NbC and Ni6Al12Mo/23 vol.% Mo at 20°C are higher than, and at 1000°C are close to the values of mechanical properties of high-temperature nickel alloy ZhS6L. It is anticipated that new particularly high-temperature resistant multilayer materials of the type of alloy/cermet, alloy/oxide will be obtained in the near future.
It should be noted that multilayer materials with thin (less than 1-2 µm) microlayers are prone to superplasticity at high temperatures as a result of decomposition of the continuous layers.
Heat conductivity and thermal expansion may also be controlled in a wide range by appropriate selection of material layers in microlaminate compositions.
Inorganic materials with a broad range of nano- and micro-sized porosity can also be deposited from the vapour phase. There exist a number of mechanisms and conditions of porosity formation at non-equilibrium condensation of the vapour phase. One of the main mechanisms of porosity formation is based on the so-called "shadowing" effect. A certain microrelief forms on the condensation surface during initiation and subsequent growth of various crystallographic faces of the nuclei at non-uniform rates. Faces and microprotrusions growing at a maximum rate screen the adjacent areas of the surface from the evaporator (vapour flow). This results in formation of inner voids. "Shadowing" effect is enhanced, if the angle of the vapour flow incidence on the condensation surface is less than 90°, or second phase particles form and grow on the condensation surface (Fig.12).
Substrate temperature Ts, condensation rate and, particularly, additives of various materials to the vapour flow allow controlling the amount, size and volume distribution of pores in the condensates.
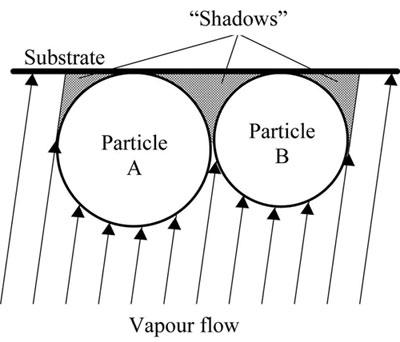 |
Fig.12. Schematic of "shadowing" zones in the vicinity of growing particles A and B on condensation surface |
Experience gained so far allows dividing all the additives into three large groups with a certain degree of conditionality, depending on the extent of their influence on development of porosity at the stage of condensate formation and subsequent heat treatment:
1. Additives practically not interacting with the main component (or components of the condensate) and remaining in the condensate volume in the form of second phase particles, for instance, ZrO2+ Ni; ZrO2+ Al2O3.
2. Additives, interacting with the main component (or components) on the interphase, and practically completely lost during condensate formation. For instance, NaCl can be such as additive for Al, Ti, Si, Zr, Al2O3, ZrO2 and TiO2 condensates. Etching of the surface proceeds, primarily on crystallite boundaries, with removal (evaporation) of reaction products.
3. Additives interacting with the main component by means of simple or
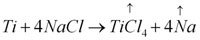
complex reactions, including those with formation of two-phase structures in keeping with the equilibrium diagrams or formation and removal of gaseous products at all the stages of condensate formation, including post heat treatments. This is a very broad group of additives for metal and ceramic condensates. For instance, for ZrO2 such additives can be Zr, B, C, refractory oxides of rare-earth elements, carbides and borides.
Fig.13a and Fig.13b show examples of structures of porous condensates based on ZrO2.
Technology variants with deposition of the vapour phase, containing additives with melting temperature below the temperature of condensation surface (Ts) of the metal and ceramic matrix, for instance Sn and Al, open up new possibilities in controlling the condensate structure. Conditions are established for formation of a thin liquid film of the additive material on the surface. Processes of liquid film interaction with the condensation surface, in particular, wetting, spreading and dissolution are actively influencing the parameters of the forming condensate structure.
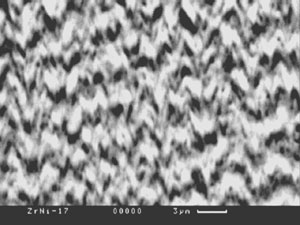 |
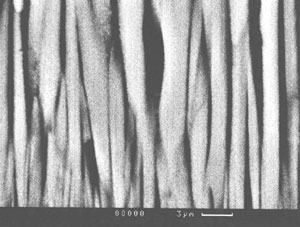 |
a) |
b) |
Fig.13. Porous structures of ZrO2(7 wt.%Y2O3) condensates with additives of Ni (a) and NaCl (b). |
"High-temperature metal - metal additive" or "refractory ceramics metal additive" compositions are characterized by formation of the metal phase segregations along crystallite boundaries, in particular, as a result of capillary impregnation and accelerated mass transfer along the defective boundaries of crystallites.
It is experimentally established that small additives of (4 - 5 vol.%) Cu and Sn have practically no influence on microhardness of TiC and TiB2 condensates, but lower their brittle fracture susceptibility.
Techniques of electron beam evaporation of dissimilar materials from independent sources, allow creating different variants of inhomogeneous (graded) distribution of the composition and respective structures along the condensates or across the condensate thickness at vapour flow deposition.
For instance, evaporation of ingots of Fe and Cr or Ni and Cu metals from two independent sources with 240 - 250 mm distance between their centers allows producing thick condensates in sheet form with a smooth variation of the composition from Fe to Cr or from Ni to Cu on a substrate located at 280 - 300 mm distance from ingot surface.
Evaporation from three or four independent sources by a preset program and subsequent condensation of vapour flows on a flat surface (disc), rotating around a vertical axis (see Fig.1b), allow controlling the composition and structure with a smooth or discrete (laminated) gradient across the condensate thickness.
Particularly attractive in terms of simplicity of the deposition process and cost-effectiveness are the variants of producing condensates with a gradient of composition and structure by evaporation from one source of mixtures of dissimilar materials, prepared in the form of composite ingots, which are described in "Basic technology" section.
Electron beam technology of material evaporation and subsequent condensation of the vapour phase can be also used to produce carbon-based materials. ICEBT developed two technology approaches:
- Direct electron beam evaporation of graphite using a "tungsten hot pool", earlier mentioned in "Basic technology" section.
- Electron beam evaporation of hard hydrocarbons, for instance anthracene C14H10 with subsequent pyrolysis and carbon vapour formation.
It is shown, in particular, that condensates with an amorphous and diamondlike phase, with nanotubes and related structures, can be produced on substrates in the temperature range of 25 - 200°C.
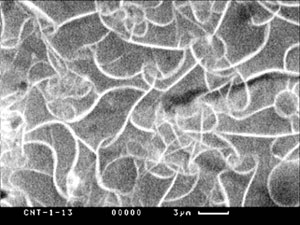 |
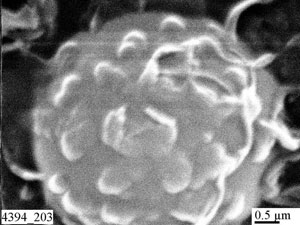 |
a) |
b) |
Fig.14. Examples of special structures of carbon condensates: nanotubes (a) and spheres (b). |
Fig.14 shows scanning electron microscopy images of tubular and spherical structures of carbon condensates. Simultaneous evaporation of carbon, metal and non-metal additives from independent sources opens up new possibilities for "engineering" carbon-based materials.
Condensates of inorganic materials separated from substrates, can be produced in the form of powder, foils, sheet, some products and even thick (10 - 20 mm) blanks for further processing.
Range of thicknesses of the above materials separated from the substrate is demonstrated in Fig.15 and Fig.16. Fig.15 shows structural schematics of variants of promising foils or sheets from microlaminate materials for sound joining of individual parts of products, as well as for fabrication of complex-shaped products from difficult-to-deform alloys, for instance, intermetallics.
Many alloys based on titanium, nickel, iron and other metals containing components with a low melting temperature, for instance, aluminium, can be produced by evaporation and condensation in the form of microlaminate materials, consisting of alternating microlayers of a low-melting component and alloy without the low-melting component.
Fig.15 shows the schematics of microlaminate foil or sheet of titanium alloys: Ti - 6 wt.% Al; Ti3Al and TiAl. Ratio of microlayer thicknesses in these materials is equal to the ratio of volume fraction of titanium and aluminium in these alloys, being 9.4, 3.2, and 1.0 for Ti - 6 wt.%Al; Ti3Al and TiAl, respectively. For instance, for Ti- 6 wt.%Al the thickness of Ti microlayers may be 3.7 µm, and of Al microlayers - 0.4 µm; for Ti3Al - 1.3 and 0.4 µm; for TiAl - 1.0 and 1.0 µm, respectively.
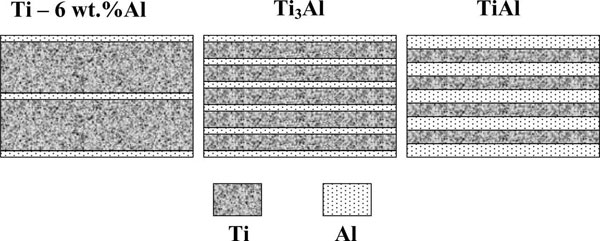 |
Fig.15. Schematic of microlaminate Ti-Al materials. |
Foils are placed between the parts being joined with application of a small external pressure, and complex-shaped blanks are produced from the sheets by deformation. At their subsequent heating up to temperatures close to aluminium melting temperature, exothermal reactions of "melting in situ" type develop, that result in formation of a sound joint or product from an alloy of the specified composition with a fine-grained structure.
Fig.16 shows a 300 x 80 x 16 mm condensate of Cu-Cr-Nb composite material, obtained by component evaporation from three independent sources and designed for subsequent mechanical and heat treatment.
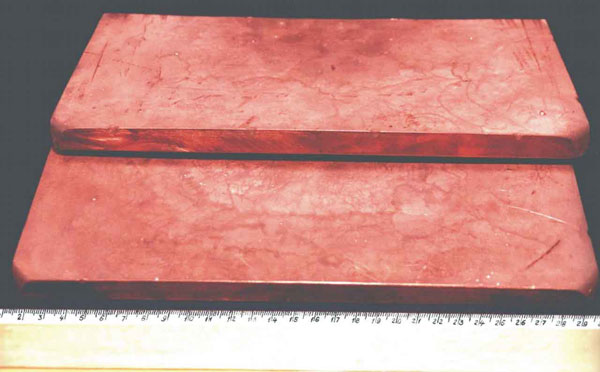 |
Fig.16. 300 x 80 x 16 mm condensate of Cu-Cr-Nb composite material
|
|